Comprehensive Guide: What is Porosity in Welding and How to Prevent It
Comprehensive Guide: What is Porosity in Welding and How to Prevent It
Blog Article
Porosity in Welding: Identifying Common Issues and Implementing Ideal Practices for Prevention
Porosity in welding is a prevalent problem that usually goes undetected till it creates significant problems with the integrity of welds. In this discussion, we will certainly discover the key factors contributing to porosity development, analyze its destructive results on weld efficiency, and review the ideal methods that can be embraced to lessen porosity incident in welding procedures.
Typical Reasons For Porosity
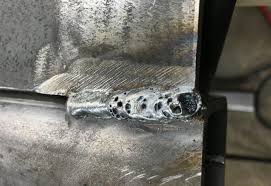
One more constant culprit behind porosity is the existence of contaminants externally of the base steel, such as oil, grease, or rust. When these impurities are not efficiently gotten rid of prior to welding, they can vaporize and come to be trapped in the weld, creating defects. Using filthy or damp filler products can introduce pollutants right into the weld, adding to porosity concerns. To mitigate these common causes of porosity, detailed cleaning of base metals, proper protecting gas choice, and adherence to ideal welding specifications are crucial practices in achieving premium, porosity-free welds.
Impact of Porosity on Weld Quality

The presence of porosity in welding can significantly endanger the architectural stability and mechanical buildings of bonded joints. Porosity produces voids within the weld steel, deteriorating its general strength and load-bearing ability. These spaces serve as stress focus points, making the weld more at risk to splitting and failure under used tons. Additionally, porosity can lower the weld's resistance to rust and other ecological elements, better reducing its longevity and efficiency.
Welds with high porosity degrees often tend to exhibit lower impact strength and decreased capability to warp plastically before fracturing. Porosity can hinder the weld's capability to efficiently transfer forces, leading to premature weld failure and potential safety hazards in critical structures.
Best Practices for Porosity Avoidance
To enhance the structural stability and top quality of welded joints, what particular actions can be implemented to reduce the event of porosity throughout the welding process? Utilizing the right welding strategy for the specific material being welded, such as changing the welding angle and weapon placement, can further avoid porosity. Routine assessment of welds and prompt removal of any issues identified during the welding process are vital techniques to protect against porosity and generate high-quality welds.
Significance of Appropriate Welding Methods
Executing proper welding methods is critical in making certain the architectural integrity and high quality of welded joints, developing upon the foundation of efficient porosity avoidance procedures. Excessive warm can lead to increased porosity due to the entrapment of gases in the weld swimming pool. Furthermore, using news the appropriate welding specifications, such as voltage, existing, and travel rate, is crucial for achieving sound welds with minimal porosity.
In addition, the choice of welding procedure, whether it be MIG, TIG, or stick welding, should line up with the details requirements of the job to guarantee optimum results. Proper cleansing and prep work of the base steel, as well as choosing the ideal filler product, are also crucial parts of proficient welding techniques. By adhering to these ideal methods, welders can lessen the threat you could look here of porosity formation and create top quality, structurally audio welds.
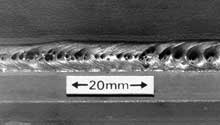
Evaluating and Quality Assurance Procedures
Testing treatments are necessary to discover and avoid porosity in welding, ensuring the toughness and sturdiness of the final product. Non-destructive screening methods such as ultrasonic screening, radiographic screening, and visual examination are frequently employed to recognize potential issues like porosity.
Conducting pre-weld and post-weld assessments is also vital in keeping quality control requirements. Pre-weld examinations involve confirming the products, tools settings, and tidiness of check out this site the workspace to stop contamination. Post-weld assessments, on the various other hand, assess the final weld for any type of flaws, consisting of porosity, and validate that it meets specified standards. Carrying out a thorough top quality control plan that includes comprehensive testing procedures and assessments is extremely important to lowering porosity issues and ensuring the overall quality of welded joints.
Final Thought
To conclude, porosity in welding can be a common concern that affects the quality of welds. By identifying the usual root causes of porosity and executing best techniques for prevention, such as correct welding strategies and testing actions, welders can make sure high quality and dependable welds. It is necessary to focus on prevention approaches to lessen the occurrence of porosity and keep the integrity of bonded structures.
Report this page